Selecting the appropriate pump for industrial applications is crucial for ensuring the efficiency, reliability, and longevity of the system. With an array of options available in the market, making the right choice can be overwhelming. Factors such as liquid type, viscosity, flow rate, temperature, and pressure requirements must be meticulously considered to match the pump to the specific industrial application. Understanding the key specifications, operational requirements, and the intended environment—such as the presence of corrosive materials or hazardous substances—can help streamline the selection process. Proper pump selection can significantly reduce operational costs, downtime, and maintenance, ensuring the continuous performance of industrial processes.

Understanding Pump Types
Pumps are classified into various categories, primarily centrifugal and positive displacement pumps. Centrifugal pumps utilize a rotating impeller to move liquid, making them ideal for low-viscosity liquids with high flow rates. They are commonly used in water supply, chemical processing, and cooling applications. On the other hand, positive displacement pumps utilize mechanical means to move fluid, making them more suitable for high-viscosity liquids. They ensure a constant flow regardless of pressure variations, making them ideal for applications involving adhesives, slurries, or heavy oils.
Assessing Fluid Properties
Before making a selection, it is essential to assess the properties of the fluid your pump will handle. Key factors such as viscosity, temperature, and chemical composition significantly impact pump performance. High-viscosity fluids may require pumps that provide higher pressure capabilities. The fluid temperature can influence the pump construction materials. Pumps designed for corrosive chemicals must incorporate compatible materials to withstand degradation over time, ensuring durability and reliability.
Calculating Flow Rate and Pressure Requirements
It is crucial to determine the required flow rate and pressure for your application in advance. The flow rate is essentially the volume of fluid moving through the system over a specified time, often measured in gallons per minute (GPM). Consider the demands of your application and the distance the fluid must travel. Pressure requirements will depend on factors like elevation changes, pipe diameter, and any potential resistance from valves or fittings. With this data, the right pump specifications can be calculated to meet your industrial needs.
Maintenance and Longevity
Analysis of maintenance requirements and expected lifespan should be a part of your decision-making process. Routine maintenance ensures optimal performance, reduces unexpected downtime, and extends the life of the pump. Selecting pumps that are designed for easy access to components allows for quicker and more affordable maintenance. Pumps designed with durable materials and sturdy construction are likely to provide longer service life, offering significant value over time. Understanding how flooded suction pumps work can also help in evaluating the most appropriate type for maintaining operational efficiency. Considering the availability of spare parts and technical support can further minimize the risk of prolonged downtime.
Energy Efficiency and Operational Costs
Choosing a pump that not only meets your operational needs but also maximizes energy efficiency is vital for minimizing costs. Energy-efficient pumps can dramatically reduce electricity consumption over their lifespan. Look for pumps with high efficiencies and consider options that include variable speed drives, which allow for flow adjustments based on the actual demand. This flexibility optimizes energy use, resulting in significant savings on operational costs.
Regulatory Compliance and Safety Considerations
Industrial operations often must comply with various industry regulations and safety standards. Understanding these requirements is essential when choosing a pump. Compliance affects everything from the materials used in pump construction to the pump’s design, ensuring it meets safety standards for the specific application. Incorporating safety features such as emergency shutoff valves can provide an additional layer of security against mishaps that might occur during pump operation.
Consultation and Vendor Selection
Consulting with experts and selecting reputable vendors can greatly enhance your pump selection process. Engaging with experienced professionals who understand the complexities of industrial needs can help identify which pump is most suited. When researching vendors, consider their reputation within the industry, product range, and post-purchase support. A reliable vendor will not only provide quality products but will also assist in addressing any queries related to installation and subsequent maintenance.
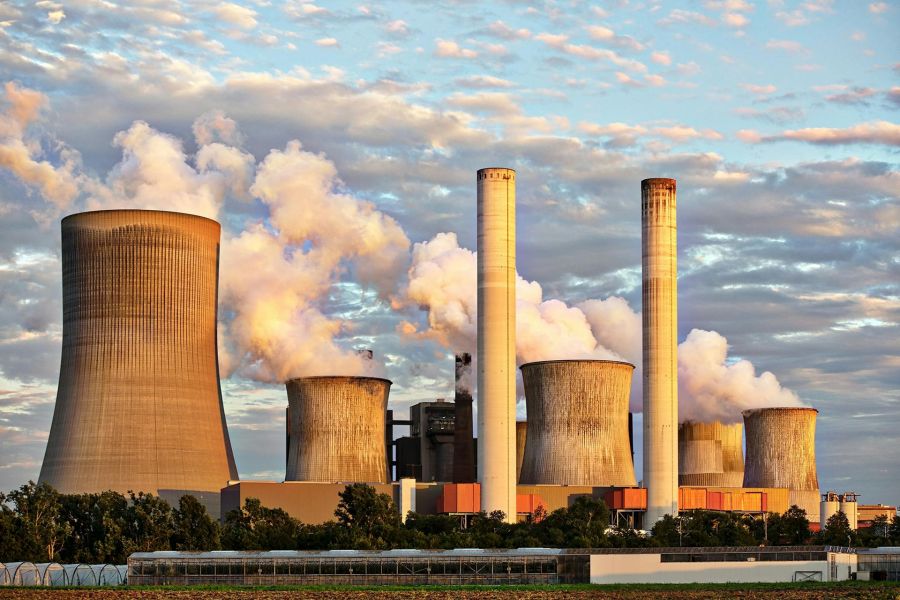
Choosing the right pump involves a comprehensive assessment of various factors, including understanding the different pump types, evaluating fluid properties, calculating flow and pressure needs, focusing on energy efficiency, and prioritizing ease of maintenance. It’s essential to also consider the environmental conditions where the pump will be used, such as temperature extremes or exposure to corrosive substances. By factoring in regulatory compliance requirements and collaborating with knowledgeable vendors or pump experts, organizations can ensure they select the optimal pump that not only meets their specific industrial requirements but also enhances operational efficiency and reduces long-term costs.
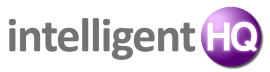
Founder Dinis Guarda
IntelligentHQ Your New Business Network.
IntelligentHQ is a Business network and an expert source for finance, capital markets and intelligence for thousands of global business professionals, startups, and companies.
We exist at the point of intersection between technology, social media, finance and innovation.
IntelligentHQ leverages innovation and scale of social digital technology, analytics, news, and distribution to create an unparalleled, full digital medium and social business networks spectrum.
IntelligentHQ is working hard, to become a trusted, and indispensable source of business news and analytics, within financial services and its associated supply chains and ecosystems