Electrical testing for components is a very important part of both making and storing electronic devices. These tests make sure that every part meets the needed standards and works properly within a system.
Given that the processes are not always straightforward, we have prepared six steps for you, whether you are a company that manufactures such components or one that uses them to build a system or a device.
Visual Inspections Come First
Just a quick glance can tell you whether a component is damaged or not. Look for physical harm like cracks, rust, or connections that are not secured or look damaged. In most cases, physical defects affect how it performs electrically and if it performs at all.
This step is simple but very important. If you are a company that works with electrical components, it is of the utmost importance to find a company that will source the right components and deliver them to you after they have gone through a process of electrical testing and without any damage.
On the other hand, if you are a manufacturer, it is crucial to implement a rigorous quality control process that will ensure that your clients, whether they are just sourcing or companies that use electrical components, don’t have any issues when they receive their orders.
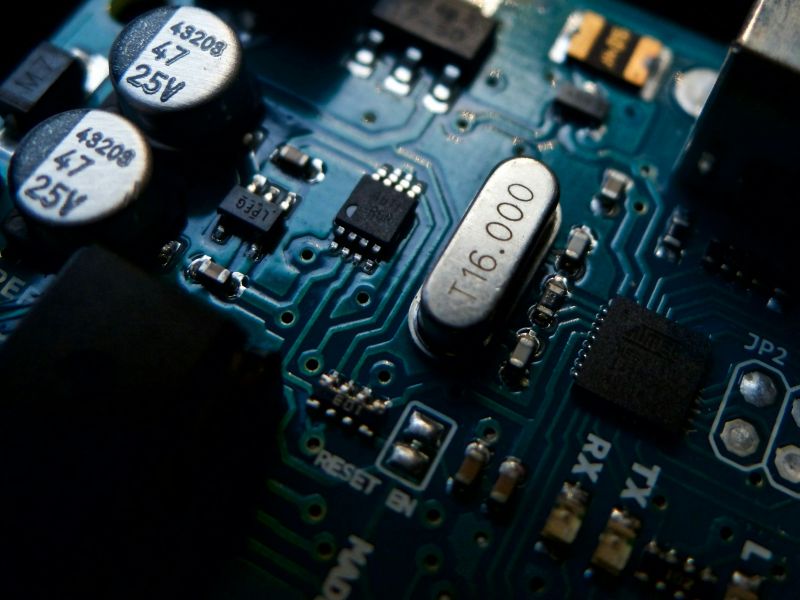
Setting Up the Test Environment
Now, you need to arrange the test situation. It means choosing the correct testing tools. You will need multimeters, oscilloscopes, function generators, etc. Attach the component to your test gear through probes or test fixtures.
Of course, each tool will produce different results so you will have to know how to analyze the readings. For example, the results from an oscilloscope will show the waveform of the signal, which can be analyzed for amplitude, frequency, and any anomalies such as noise or distortion. A multimeter, on the other hand, can measure voltage, current, and resistance, providing more static readings compared to the dynamic waveform data from the oscilloscope.
Functional Testing
Functional testing is about checking if the component can carry out its planned function. This could involve tests like signal integrity testing, frequency response examination, or load checks. For instance, an operational amplifier (op-amp) can be tested for gain, bandwidth and its reaction to various input signals. Usually, this stage requires complicated test arrangements and specific tools such as signal generators and spectrum analyzers.
Voltage and Current Testing
Even if the component functions and carries out its intended purpose properly, it still needs to be stress tested. In other words, this entails how the component will perform in the long term under load.
Voltage and current tests are very important because they confirm how the component performs in real operating situations. You can use an oscilloscope or a multimeter to measure the voltage across the component and also observe its current flow.
After noting these values, compare them with expected measurements to check if this part works properly or not. As an example, when dealing with a diode, you have to verify the forward voltage drop and reverse leakage current. Such examinations ensure that the component will operate as expected once it is placed within a circuit.
Insulation Resistance Test
The insulation resistance test is about the sturdiness of the material used for insulation in the component. This test has a big role in making sure safety is good and short circuits don’t happen. A supply with high voltage gets put on the component, and we measure how much resistance there is between the insulating material and conductors.
The resistance needs to show a very high value, which means the insulation is good. This test is important for parts that work with high voltages because it confirms they will not break down when under pressure.
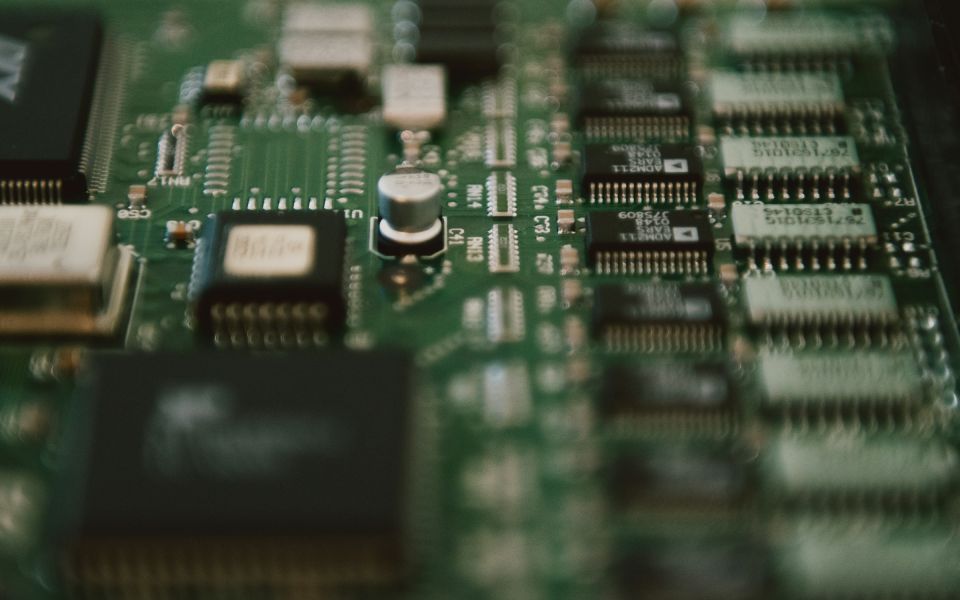
Capacitance and Inductance Measurement
Measuring the value of capacitance and inductance for capacitors and inductors is very important.
These measurements confirm that components are within their specified values. A capacitance meter, or LCR meter, can be employed to carry out such tests. Timing and filtering applications are highly dependent on components that require exact measurements of capacitance and inductance for the correct circuit function.
Wrap-Up
The failure of an electric component is a serious problem. From 2009 to 2019, there were nearly 15 million vehicles recalled due to some issue or another. To that end, testing is very important to guarantee the excellence and capability of electronic components.
Actions like visual inspections, preparing the environment for tests, functional checks, voltage and current tests, insulation resistance tests plus measuring capacitance and inductance are vital. Testing helps to lower failure rates, save money, and confirm safety rules.
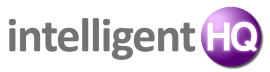
Founder Dinis Guarda
IntelligentHQ Your New Business Network.
IntelligentHQ is a Business network and an expert source for finance, capital markets and intelligence for thousands of global business professionals, startups, and companies.
We exist at the point of intersection between technology, social media, finance and innovation.
IntelligentHQ leverages innovation and scale of social digital technology, analytics, news, and distribution to create an unparalleled, full digital medium and social business networks spectrum.
IntelligentHQ is working hard, to become a trusted, and indispensable source of business news and analytics, within financial services and its associated supply chains and ecosystems