Injection molding has been a cornerstone of manufacturing for decades, playing a pivotal role in producing high-quality, precision parts across a variety of industries. However, as technology evolves, the demands of the market have shifted, and businesses are increasingly expecting faster turnaround times, cost efficiency, and superior product quality. To meet these new expectations, injection molding services must evolve.
Companies that can integrate modern innovations into their processes will not only stay competitive but will also unlock new opportunities for growth and advancement. This post will delve into the necessity of adapting to modern innovations in the injection molding industry, highlighting key areas of change and their benefits.

The Role of Automation in Injection Molding
One of the most significant innovations transforming injection molding services is automation. As industries strive for efficiency, automation has become an indispensable tool in the injection molding process. Robotic systems can now handle everything from material handling to assembly, reducing human error and speeding up production timelines.
Automation also facilitates the use of advanced technologies like predictive maintenance, which helps anticipate and mitigate machine failures before they occur. This means injection molding services can offer more reliable, consistent products with fewer interruptions. For businesses, this translates to lower operational costs and an ability to scale production without sacrificing quality.
Advances in Materials Science
Modern injection molding is no longer limited to traditional plastics. The field has witnessed significant advancements in materials science, allowing for the use of innovative materials such as bio-based plastics, composites, and high-performance polymers. These materials offer a range of benefits, including enhanced durability, sustainability, and specialized properties tailored to specific applications.
Injection molding services that adapt to these new materials can offer customers more customized and cutting-edge solutions, meeting the growing demand for eco-friendly products and products designed to withstand extreme conditions. The ability to work with a broader range of materials will be crucial for any injection molding service looking to stay relevant in an evolving market.
Customer-Centric Services and Customization
As customer expectations shift towards greater personalization and bespoke products, injection molding services must adapt by offering more tailored solutions. Advanced technology has made it easier for manufacturers to produce customized parts in smaller batches while still maintaining cost efficiency. Companies for injection molding that integrate flexible, customer-centric services—such as offering quick turnaround times, personalized designs, and even on-demand production—will have a significant advantage over those that adhere to traditional, one-size-fits-all approaches. In a world where customers are seeking unique, high-quality products, the ability to adapt to these demands is essential for staying relevant.
3D Printing and Prototyping Integration
Another modern innovation that is reshaping the injection molding industry is the integration of 3D printing technology. 3D printing, or additive manufacturing, is often used in the prototyping phase of product development. By creating prototypes through 3D printing, businesses can rapidly iterate designs without the need for expensive molds or tooling. Injection molding services can benefit from this technology by offering faster, more cost-effective prototyping options to clients.
The combination of 3D printing and injection molding can lead to more complex geometries and customized parts that were previously impossible or cost-prohibitive to produce. By integrating 3D printing into their processes, injection molding services can enhance the overall product development cycle, providing value to clients from the initial design phase through to mass production.
Sustainability in Injection Molding
Sustainability has become a significant focus across all industries, and injection molding is no exception. Consumers and businesses alike are increasingly concerned with the environmental impact of the products they use. Injection molding services must adapt to these concerns by adopting sustainable practices, such as reducing waste, using recycled materials, and optimizing energy consumption during production.
Innovations in biodegradable and recyclable materials are allowing manufacturers to meet the demand for environmentally-friendly products without sacrificing the benefits of injection molding, such as speed and cost efficiency. By integrating sustainability into their operations, injection molding services can appeal to the growing eco-conscious consumer base while also contributing to a more sustainable manufacturing industry as a whole.
The Importance of Digitalization and Data Analytics
The ability to harness data is crucial for staying competitive. Injection molding services are increasingly turning to digitalization and data analytics to improve their operations. By collecting and analyzing data throughout the production process, companies can gain valuable insights into machine performance, product quality, and material usage. This allows them to make more informed decisions, reduce defects, and improve the efficiency of the manufacturing process.
Digital tools like real-time monitoring and simulation software also enable better process control, leading to enhanced product quality and consistency. In an industry where precision is paramount, the ability to leverage digital technologies and data is quickly becoming a necessity for companies looking to remain competitive in a rapidly evolving marketplace.

Injection molding services must adapt to modern innovations to remain competitive in today’s fast-paced and ever-changing manufacturing landscape. By embracing automation, advanced materials, 3D printing, sustainability, digitalization, and customer-centric approaches, companies can offer superior products, improve efficiency, and meet the growing demands of the market. Those who fail to adapt risk falling behind as industries move towards more innovative and dynamic production methods. To thrive, injection molding companies must be agile, forward-thinking, and committed to integrating new technologies that will drive growth and success in the years to come.
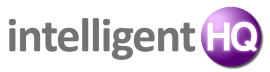
Founder Dinis Guarda
IntelligentHQ Your New Business Network.
IntelligentHQ is a Business network and an expert source for finance, capital markets and intelligence for thousands of global business professionals, startups, and companies.
We exist at the point of intersection between technology, social media, finance and innovation.
IntelligentHQ leverages innovation and scale of social digital technology, analytics, news, and distribution to create an unparalleled, full digital medium and social business networks spectrum.
IntelligentHQ is working hard, to become a trusted, and indispensable source of business news and analytics, within financial services and its associated supply chains and ecosystems