If you outsource product production to a custom manufacturing firm, quality assurance is important. You need to be confident that the company you pay to manufacture products for you is able to do so in a timely manner, without compromising quality. There are many firms offering custom manufacturing services today, so finding one with strict quality control policies in place should not be difficult. This post will now explore this topic in more detail and tell you about some of the things that you can do to manage quality assurance and ensure the company you work with produces quality products for you.
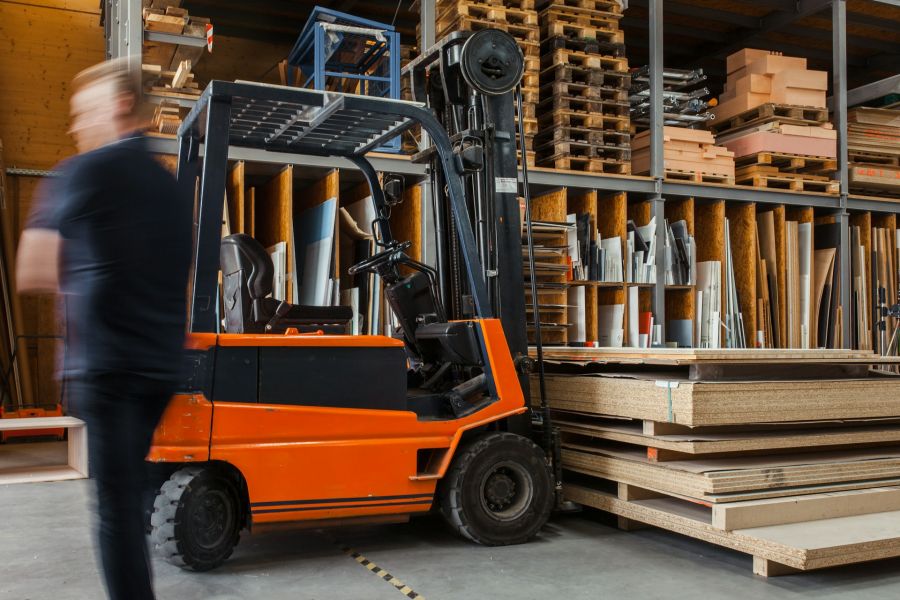
Exceptional Quality
If a company has a history of producing high-quality products, you can trust them to have strict quality control policies in place. For example, the experts from Fieldtex say on their site that they have a skilled team of over 125 operators working for them, and have a history of producing quality products that goes back to the 1970s. You can visit Fieldtex Products to learn more about them. You should look for a custom manufacturing partner with credentials and a history like this. Most businesses will advertise this information on their website’s homepage like Fieldtex does.
Read Reviews
A custom manufacturer’s reviews can tell you a lot about them and the quality of the products they produce. If you have any doubts or concerns about a specific manufacturer’s products, go straight to their reviews and see what past and present customers have to say. Something to note about reviews is that if a business has none, that doesn’t necessarily mean their products aren’t worth buying. Sometimes a total absence of reviews actually means a business’s clients have nothing negative to say about them. A business’s star rating can also give you some insight into product quality.
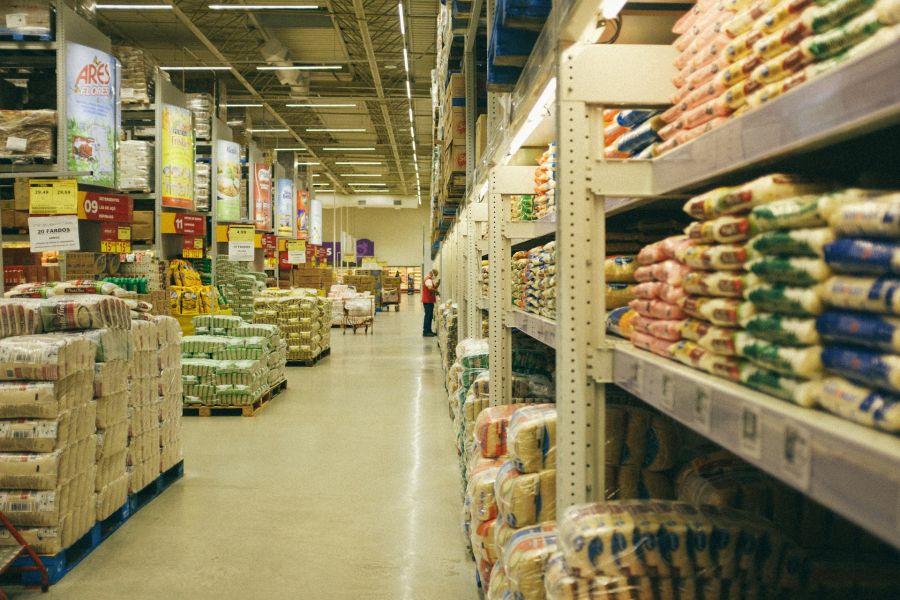
Employee Training
Employee training is a great way to ensure that your employees know what a good product does and doesn’t look like. It is especially important to train employees in spotting defective goods if they handle more stock than you do. The most effective way of training them is to do it yourself, passing knowledge you have learned about the products you sell down to them. If you do not have the time or ability to do this, you can hire an external training provider to do it for you.
Quality Standards
Make your idea of quality clear to your chosen manufacturing partner from the first minute you meet them. Don’t make the mistake of being vague as it relates to what you want. If you do not tell your supplier what you deem to be high-quality, they are never going to be able to satisfy your needs. Make sure that in addition to being clear about what you want, if your chosen supplier sends you products you consider unacceptable, you get in touch with them as soon as possible to complain, so they can either refund or reimburse you.
Managing quality assurance when you run a business that buys its products from a custom manufacturer no longer has to be difficult. With the advice given here, you can buy stock confidently and with no stress.
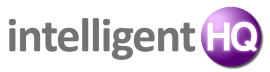
Founder Dinis Guarda
IntelligentHQ Your New Business Network.
IntelligentHQ is a Business network and an expert source for finance, capital markets and intelligence for thousands of global business professionals, startups, and companies.
We exist at the point of intersection between technology, social media, finance and innovation.
IntelligentHQ leverages innovation and scale of social digital technology, analytics, news, and distribution to create an unparalleled, full digital medium and social business networks spectrum.
IntelligentHQ is working hard, to become a trusted, and indispensable source of business news and analytics, within financial services and its associated supply chains and ecosystems